During production the integrity of the reproduction of artwork is monitored by making comparisons, for example, original to its copy or proof to presswork. The two colored objects are referred to as a metameric pair if they match under at least one combination of illuminant and observer and not match under at least one combination of illuminant and observer. They must also have different spectral response curves.
So, the phenomenon of metamerism begins with comparing a pair of colored objects. For example the color of the back door of this truck compared with the color of the rest of the truck.
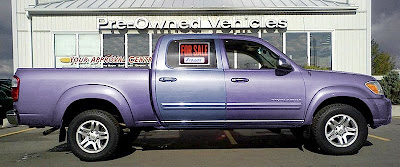
In the truck example the pigments used in the paint were not the same for the back door compared with the rest of the truck. The two colors would have matched under the artificial lighting that was used when the door was painted. However, under sunlight conditions the door and body no longer match causing "metameric failure."
In this case metameric failure is a benefit to the prospective customer since it warned that the door was painted at a different time from the rest of the truck. Possibly it had been damaged and subsequently repaired. Unfortunately the effect of metameric failure in print production usually causes problems rather than benefits.
How metameric failure impacts print production
There are four types of metameric failure commonly encountered in print production.
Sample metameric failure This is the most common cause of color matching problems. The truck example above is an example of sample metamerism. Because proofs and press sheets form metameric pairs, this problem typically shows up when presswork matches the proof in the light booth at press but no longer match under the lighting conditions where the presswork will normally be used, e.g. a package in a store, or brochure in a home environment. Other examples of sample metameric failure include product samples (e.g. fabric) compared with their reproduction in proofs, presswork, or computer displays. Or process color screen tint builds. They may match under one lighting condition but not another. Sample metameric failure can also happen if two prints using very different technologies - such as offset print vs silkscreen print - are compared under different lighting conditions.
Observer metameric failure This can happen because of differences in color vision between observers. Although the common cause is colorblindness, it is not uncommon among "normal" observers. As a result, two spectrally dissimilar color surfaces may produce a color match for one person but fail to match when viewed by a another person. Observer metameric failure is the reason there were 31 individuals tested to derive the original 1931 "standard observer" values adopted by the ISO and that are still used today as the basis for the majority of color science.
Field-size metameric failure This occurs because the relative proportions of the three light sensitive cone types in the retina of the eye vary from the center of the visual field to the periphery. The result is that colors that match when viewed as very small, centrally fixated areas may appear different when presented as large color areas. This is the reason why color painted on a wall may appear different than the paint chip used to select the color even though they match when the chip is placed on the wall. In print production field-size metameric failure typically occurs when small PMS swatchbook samples are used to specify a PMS color that will cover a large press sheet area.
Geometric metameric failure Normally, material attributes such as translucency, gloss or surface texture are not considered in color matching. However here, identical colors appear different when viewed at different angles, distances, light positions, etc. Geometric metameric failure is most often seen when using metallic inks or paper, and specialty ink coatings or papers.
Tips for dealing with metameric failure
1. Be aware that it exists and may be the "simple" issue causing any color match issues.
2. If color needs to align across different lighting conditions choose pigments carefully or make the ink formulator aware of that requirement.
3. Control your lighting conditions - both for producing prints, final viewing (where possible), and for critical evaluation. The industry standard light source is referred to as "D50" or "D65" (5,000° Kelvin (North America), 6,500° (Europe).
4. Invest in PIA/GATF RHEM light indicators for everyone in the production chain that is involved in evaluating and approving color. RHEM light indicators are small (2" x 3/4") paper stickers with a unique printed design that uses metameric failure to indicate whether or not the viewing conditions are 5,000° K or not.
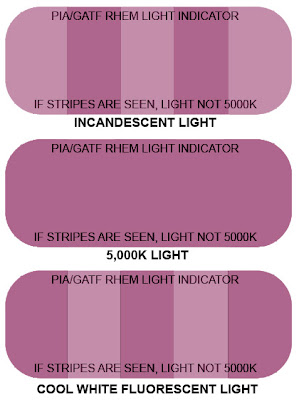
The stickers can be affixed to proofs or simply carried in a protective wrapper in purse or wallet.
5. Printshops should have viewing areas away from the press that allow print customers to view the presswork under typical lighting conditions (fluorescent and incandescent).
6. Be sure that all instruments (e.g. spectrophotomers) that are used for color evaluation are set to the same standard illuminant, D50 or D65, and same observer angle (typically 2°).
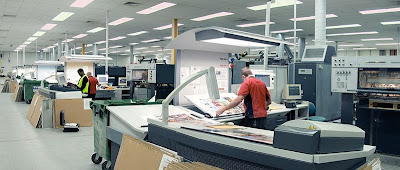